It was only last year that the use of silicon for solar cells outdistanced – or perhaps “outarea-d” – that for semiconductors. Whichever way you look at it, that’s remarkable: chips are tiny, even though they’re made by the thousand, while solar panels are large objects, intended to cover a roof rather than fill a little gap in a motherboard.
Yet it’s taken this long – despite solar panel use growing at 40% annually over the past decade – to get to the stage where we are starting to make more silicon to generate energy than to use it up. Sometimes, you have to wonder at our priorities as a species. But you can have so much more fun with a computer than with a solar panel. At least until the power runs out. Then you want both.
If you listen hard enough, you can hear the signs of what we could call “energy stress” all around. Oil prices aren’t coming down. Power suppliers keep hiking their fuel prices, sighing along with their customers (yet somehow increasing profits). And, mirabile dictu, the Sun newspaper this week came out in favour of being green, saying: “Too many of us have spent too long in denial over the threat from global warming. The evidence is now irresistible …” And there you were thinking that red-top newspapers had green colour blindness.
So solar is beginning to look increasingly attractive, because – unlike nuclear power – you can getyour own, and as Ashley Seager showed in this paper on Monday (Soaring energy costs make solar power a bright idea, September 11), make an economic return on capital.
Thus amid all the gloom, there are smiles on the faces of people who work in the industry, such as Charles Gay, a 30-year veteran of the solar business. He’s general manager of the solar panel business at the wonderfully-named Applied Materials (a moniker so generic it sounds like James Bond’s front company). He’s full of optimism about the future of his sector: “The big companies take this seriously – it’s a genuine growth area.” The OPEC oil embargo of 1973 kickstarted the business, and since then it’s gone up and down, but right now is on the up: Japan and China are big users, and following another summer in which California’s power business sunk to its knees as everyone turned on the air conditioners, Arnold Schwarzenegger (turning out to be the ideal politician, more interested in pragmatism than party politics) has initiated a scheme to put 3kW of photovoltaic capacity on 1m Californian rooves – to generate as much electricity as three power plants – in the next 10 years.
But panel costs still remaintoo high for us to rush out for them. Yet what’s the bottleneck? A tug-of-war between chip plants and solar panel makers? Not precisely, explains Gay. The problem is supply; but unlike chip manufacturing, where prices wax and wane as new generations of chip foundry come along, we can’t make enough silicon to meet demand. “Purifying silicon is like building a petroleum cracking plant,” says Gay. “It takes two or three years.”
And while the pub bore will tell you that silicon is the second most plentiful element in the Earth’s crust, the problem is wrestling it from the grip of the oxygen it’s bound to. Just as with aluminium (which has to be electrolysed from bauxite), the principal cost of silicon’s manufacture is electricity.
Thus the world’s biggest silicon manufacturing plants are in Scandinavia and China, where hydroelectric power is plentiful. (China is a big fan of solar power too.) I like the circularity: renewable energy being used to create the raw material for another renewable energy source. Yes, dams create problems of their own, and silicon is toxic. But if it’s a choice between that and pushing a plough, I’ll take the first one every time.
13.03.2007
Energy Stressed? Take Some Silicon and Lap Up the SUN
Other News
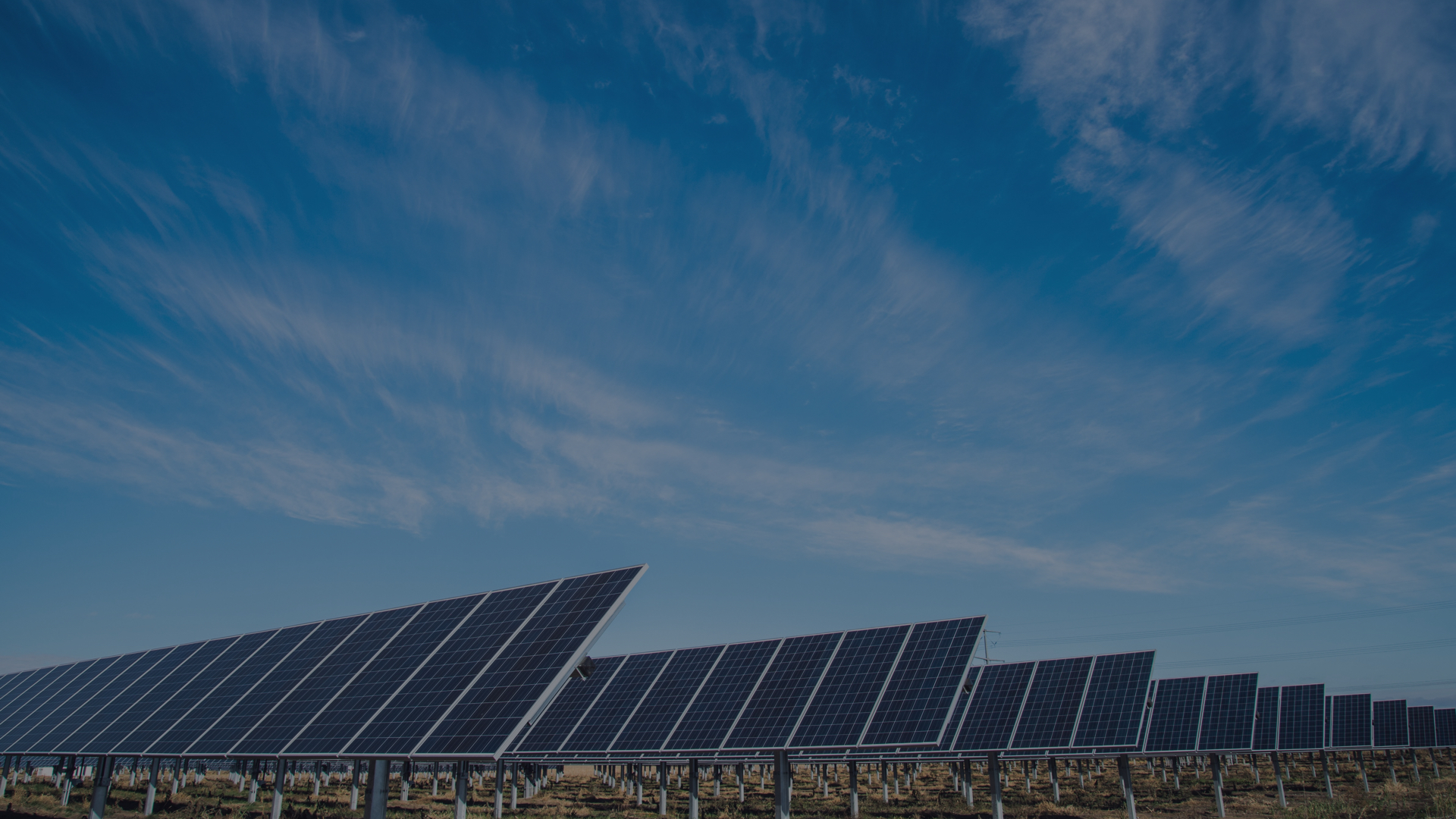